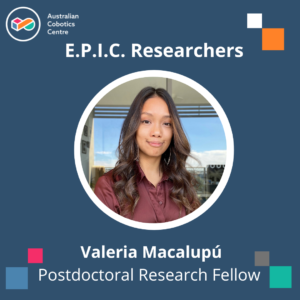
Valeria Macalupú is a Postdoctoral Research Fellow in the Human-Robot Interaction program (P2), sessional educator and interdisciplinary designer at Queensland University of Technology.
We interviewed Valeria recently to find out more about why she does what she does.
Tell us a bit about yourself and your research with the Centre? Include the long-term impact of what you are doing.
I am a Postdoctoral Research Fellow in the Human-Robot Interaction program (P2). I am also an industrial designer at heart, which was my bachelor’s degree in Peru. My research background is in co-designing social robots, particularly for aged care and service environments. Over the last 5 years, my research journey has focused on how design impacts robot acceptance, interaction, and integration in human spaces.
At the Centre, I contribute to shaping how cobots are designed for real-world use, ensuring they align with human needs, habits, workflows, and expectations. The long-term goal is to develop truly integrated robots into workplaces and society, making them more intuitive, accepted, and useful.
Why did you decide to be a part of the Australian Cobotics Centre?
I was drawn to the Centre because of its collaborative and interdisciplinary approach to robotics. My work sits at the intersection of design, robotics, and environment interaction, and the Centre provides a unique space to bridge these fields. The amazing work done at Program 2 allowed me to extend my knowledge across aged care and pedagogical areas to healthcare and manufacturing ones, which fills me with excitement.
Being part of a team that includes engineers, designers, and industry partners allows me to explore how we can design robots that truly work for people, not just technologically but socially and practically.
What project are you most proud of throughout your career and why?
One of my proudest projects is HELPII, where I contributed to researching and designing a social service robot for aged care. The fantastic team at the QUT Centre for Robotics (QCR) created this robot and developed the technology. We were invited to find a real market opportunity in aged care, and through multiple studies and visits to residential aged care facilities, we determined the best applications and tasks for the robot. I highlighted key design decisions that support understanding the real needs of staff and residents and ensuring the technology fits into their daily lives.
What made it meaningful was collaborating across disciplines and bringing the team together to see that robot design comes with many considerations, from colour and material theory to environmental systems and emotional design. Working with roboticists, architects, and aged care professionals to bridge gaps in communication and expectations was a brilliant experience. Particularly visiting and studying a facility with 10 robots in place! This project solidified my passion for HRI and showed me the real-world impact of thoughtful design.
What do you hope the long-term impact of your work will be?
I want to reshape how we design and implement robots in the home, workplaces and public spaces. Technological advancements often drive robotics, but thoughtful design plays a crucial role in ensuring robots are functional, intuitive, and widely accepted.
My goal is to establish better design, adoption, and co-habitation practices, ensuring robots are not just tools but seamlessly integrated into human environments. I hope my work lays the foundation for robots that feel as natural in our world as any other tool we use today.
Aside from your research, what topic could you give an hour-long presentation on with little to no preparation?
I could probably talk about design and decor in everyday life and how subtle decisions in design shape our interactions, experiences, and even behaviours. Design is everywhere, from how we intuitively use technology to how spaces influence our emotions. Otherwise, I could go on and on about Harry Potter and Lord of the Rings.