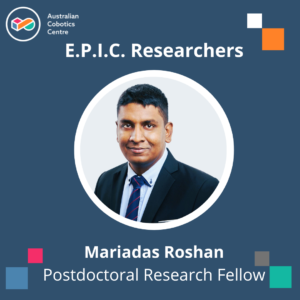
Mariadas Roshan is a Postdoctoral Research Fellow in the Quality Assurance and Compliance program and is currently involved in an industrial-based cobot automation project.
We interviewed Mariadas recently to find out more about why he does what he does.
Tell us a bit about yourself and your research with the Centre? Include the long-term impact of what you are doing.
I am a Postdoctoral Researcher in the Quality Assurance and Compliance program (P4) at the Australian Cobotics Centre, based at Swinburne University of Technology. I hold a Bachelor’s degree in Mechatronics Engineering and completed my PhD in Robotics, where I focused on developing autonomous ultrasound imaging systems using computer vision and collaborative robots.
At the Centre, my research focuses on integrating collaborative robotics and intelligent vision systems into real-world manufacturing environments to improve quality control, ensure compliance, and enhance human-robot collaboration. I am currently working on an industry-based project that aims to automate and optimise quality assurance in manufacturing. In parallel, I’m involved in projects exploring how collaborative robots can be used for both autonomous and teleoperated ultrasound imaging in healthcare.
I believe that the potential of robots is still underutilized or not fully understood in many real-world applications. My long-term goal is to help bridge that gap, by driving the adoption of robotics across diverse sectors like manufacturing and healthcare. This will ensure that these technologies are accessible, effective, and aligned with real human needs.
Why did you decide to be a part of the Australian Cobotics Centre?
I’ve always had a passion for robotics, which led me to pursue a Bachelor’s degree in Mechatronics Engineering and later a PhD in Robotics. During my PhD, I became increasingly aware that much of the research being done either didn’t reach industry or lacked practical impact. I’ve always been motivated by research that addresses real-world problems and delivers tangible solutions to industry challenges.
When I was looking for a postdoctoral opportunity, the Australian Cobotics Centre stood out because of its strong focus on implementing collaborative robotics in Australian manufacturing. The Centre’s mission aligns closely with my own values, ensuring that cutting-edge research leads to meaningful, real-world outcomes. What also attracted me was the Centre’s diverse, interdisciplinary team, which considers not only the technical aspects of cobot implementation but also the human, organisational, and design perspectives. It’s an environment where I can contribute while also learning and growing alongside experts from various fields.
What project are you most proud of throughout your career and why?
One of the projects I’m most proud of took place during my PhD, when I worked part-time as a mechatronics engineer at a start-up mask manufacturing company at the height of the COVID-19 pandemic. At the time, Australia had only one local mask production facility, and the manufacturing machines were imported, which meant we had very limited technical support. I was part of the team responsible for designing and deploying the automation of the mask production process, an effort that was both urgent and technically demanding. Despite the limited resources and high-pressure environment, we successfully established a functioning production line. Even though regulatory compliance wasn’t my core area, I also took on the responsibility of overseeing lab testing and navigating the TGA approval process, as our team lacked expertise in that area. It was a demanding but incredibly rewarding experience, especially knowing the direct impact it had during a national health crisis.
Another project close to my heart is one I’m currently involved in is a teleoperated and autonomous collaborative robot system for ultrasound imaging. The goal is to create a solution that can support healthcare professionals and provide better access to diagnostic services in regional and remote communities. I’ve been contributing to this outside of my main projects because I strongly believe in its potential to make a real impact in the healthcare sector.
What do you hope the long-term impact of your work will be?
Through my experience working on industry-focused projects, I’ve come to realise that many companies, especially SMEs, are still hesitant to adopt robotics due to factors like perceived risk, high initial investment, and a general lack of awareness, particularly in Australia. I hope the long-term impact of my work will be to bridge that gap by demonstrating the real-world value and practicality of robotics across industries.
I want to support wider acceptance and adoption of robots, not just in manufacturing but also in underexplored areas like healthcare, where robotics can have a significant impact. Ultimately, I aim to contribute to a future where robotics is seen not as a complex or risky investment, but as a valuable and accessible tool that can enhance productivity, improve safety, and create better outcomes for people and businesses alike.
Aside from your research, what topic could you give an hour-long presentation on with little to no preparation?
Without a doubt, cricket! I’ve been a huge fan since I was young. While I don’t get as much time these days to watch full matches, I still closely follow scores, player stats, and expert analyses. I especially enjoy watching podcasts and technical breakdowns of games, where strategies, player skills, and match dynamics are discussed in depth. Whether it’s team strategies, player performance trends, or predicting outcomes based on pitch conditions and line-ups, I could easily give a detailed and passionate talk on any aspect of the game.